After reading “New Hubs Arise to Serve ‘Just in Case’
Distribution,” I wanted to learn more about this idea of Just-In-Case supply chain management. Personally, I am a planner,
I like to always be prepared, and I like to avoid risk, so this sounded like my
type of supply chain management. Below
is some information I found about this theory.
Chris O’Brien wrote the article “Build Resilience into Your
Supply Chain,” where he describes Just-In-Case as a type of proactive crisis
management. He explains that natural
disasters and other unforeseen events have shed light on weaknesses in
traditional supply chains, and he advocates developing plans to deal with these
events before they occur and do irreparable damage to your organization. He stresses that when companies are separated
from their customers or suppliers, it’s easy for competitors to move in and
take over.
O’Brien says, “Global companies with
high-value, high-demand products coming from multiple locations are the most
likely to need a mitigation strategy.”
Specifically, he mentions retailers and name-brand pharmaceuticals
because their customers demand a constant supply of goods. O’Brien suggests creating a supply chain map
to identify “chokeholds” related to suppliers, inventories, technology or
transportation. He also advocates asking
questions about one’s supply chain to identify where problems could occur and
what could be done to mitigate them. He
does concede that “complete redundancy is cost prohibitive,” and that not every
step of the supply chain needs to be backed up.
Below is a graphic from O’Brien’s
article that indicates the top perceived threats for supply chain managers (as
reported by them).
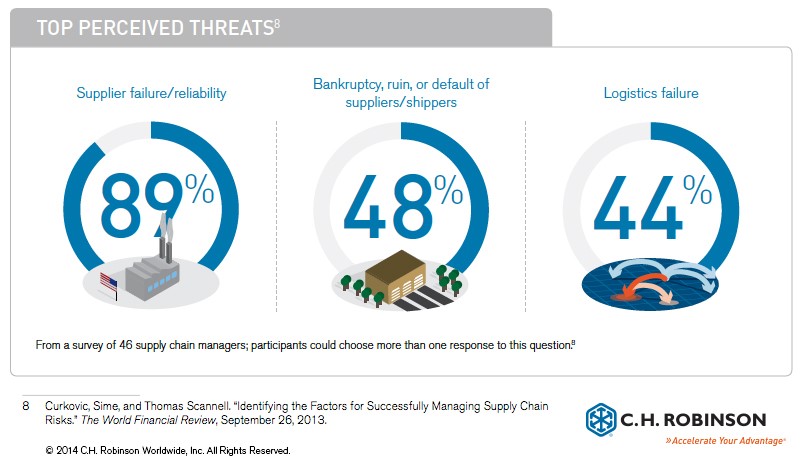
I appreciated O’Brien’s explanations on
how to begin to execute a Just-In-Case strategy, and I
began to think of industries that could benefit from this idea – like road salt for
winter storms.
While continuing my search, I found that Edith Simchi-Levi
wrote “3 Trade-offs of Just-in-Case and Just-in-Time Supply Chain Strategies”
as a response to our class reading mentioned above. In the article, Simchi-Levi reiterates many
of the ideas from our article, but instead of focusing on mitigating risk, she concentrates
on rising transportation costs. These
costs make locating distribution centers closer to customers more
attractive. The three key ideas
discussed are:
1. Increasing costs of the “final leg” of shipping make
regional distribution centers more desirable.
2. Companies shift
from “off-shoring” to “near-shoring” to move sourcing and production closer to customers.
3. As manufacturing moves closer to customers, plants need
to become less specialized and more flexible to
meet the needs of customers.
I found Simchi-Levi’s ideas interesting, but it seemed like
she was overlooking the crisis mitigation aspect of Just-In-Case. However, her three key ideas make a lot of
sense and actually relate to some of our other reading for the week.
While I continued searching for information on Just-In-Case,
I found one last article titled, “Should You Stock Up On Chocolate Bars Because Of
Ebola?” The article explains that half
the world’s cocoa comes from Ivory Coast and Ghana, which are next to
the center of the Ebola outbreak.
Apparently, cocoa prices are slowly rising, and some analysts fear a
major spike in the cost of cocoa, which would raise the cost of all chocolate
goods. With this information, should
companies like Lindt and Hershey’s begin creating Just-In-Case supply
chain plans to mitigate the risks of rising cocoa costs or a major shortage of
cocoa? Or, are the risks too small to
warrant major investments in alternate supply chains?
Questions:
1. If you were in the chocolate business, what would you do
with this minor risk looming?
2. What products or
industries do you think would most benefit from a Just-In-Case philosophy?
Sources:
Did you know you can create short links with LinkShrink and make cash from every click on your short links.
ReplyDelete