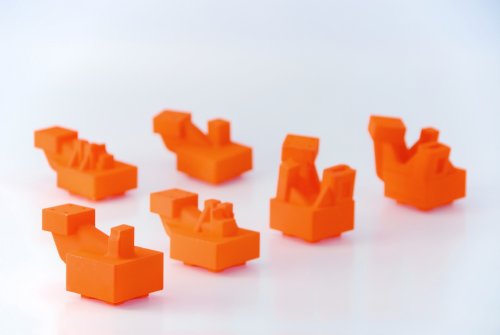
RapidFit+ (a product of Materialise) has used 3-D printing technology to transform the quality assurance process for manufacturers, enabling the production of previously difficult or even unthinkable designs and making the entire process cheaper, faster and more responsive to design changes.
I believe that this technology has been primarily used in the automotive industry, so far. In these supply chains, smaller manufacturers produce parts that are put into larger parts by other manufacturers, which may be added to even larger components by another manufacturer, and so on until the final components are installed by the automaker in a vehicle. These supply chains can be incredibly complex, and if one manufacturer anywhere on the chain produces parts outside of a very strict set of specifications the whole system quickly falls apart.
In the past, individually machined (and very expensive) aluminum or steel relief-molds were used by manufacturers to check the accuracy of parts being produced. When a part was produced, it could be slipped into the mold and checked for accuracy. Today, the introduction of new hyper-precise 3D printing technology and the ubiquity of the Internet mean that custom 3D printed objects can be used to verify parts as they move though the manufacturing process.
At RapidFit+, an original equipment manufacturer (OEM) can use an online platform to upload 3D and engineering data who then works out a precise rig that can accurately check the dimensions of the finished part within +/- 0.05 mm. At any time the OEM can use the online platform to approve the design or make changes to the parts if necessary. Once approved, a fixture is produced and the precision calibration units are 3-D printed (These are orange things you see in the photo at the top of this post.) and sent to the part manufacturer.
This technology brings numerous advantages to the supply chain. As previously stated, these quality assurance rigs were traditionally made from a solid block of metal. Aside from the huge expense of creating it, these rigs were only accurate for a single part, possibly on a single model of car. With the adoption of 3-D printing, adjustments can be made when small changes are ordered, or for similar parts between different models. Further, these new quality assurance rigs can be produced cheaply, quickly, durably (tests have shown that even after 10,000 cycles wear is limited to only a few microns) and as previously stated the OEM can send design changes in real time. And because the rigs are built on a modular structure, and only the precision "locators" are custom printed, a rig can be configured in multiple ways for multiple parts depending on needs of the part manufacturer.
Currently, RapidFit+ uses this technology in-house, but it is not impossible to see a future where individual part manufacturers invest in 3-D printing technology and their customers are able to upload design specifications directly.
Question: Within the field of supply chain management, for what other applications could 3-D printing technology be suitable?
RapidFit+ using 3D printing to check mass produced parts
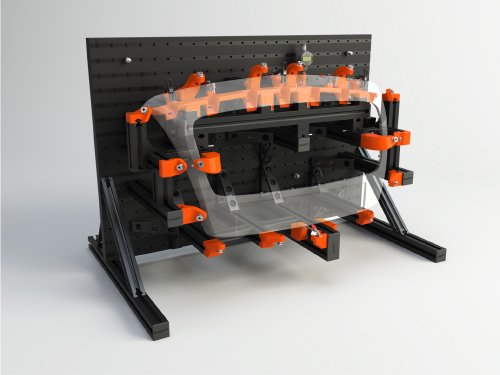
Quality Assurance makes sure the project will be completed based on the previously agreed specifications, standards and functionality required without defects and possible problems. It monitors and tries to improve the development process from the beginning of the project to ensure this. It is oriented to "prevention".
ReplyDeletequality assurance
This is so interesting blog. You are best listing knowledge provide at this site. I am very excited read this nice article. We offers changeparts .
ReplyDelete